Design
With a clean sheet of paper and no monetary constraints, one has the luxury of thinking outside the box … well, in fact, there was no box!
Perfecting the wheel … as a juxtaposition to musical nirvana.
Building a perfect oval wheel rather than perfecting the round wheel … as it is with the amplification of recorded music.
The finest amplifier manufacturers today are simply making oval wheels when we know deep down we really need a round wheel to porperly work!
Tenor has embarked on a life’s work to correct this short coming. Tenor has achieved the impossible by re-inventing the amplifier - the only amplifier capable of presenting recorded music with zero perceived distortion!
A live acoustic instrument, let’s say a horn instrument, when played through a typical stereo system does not sound exactly right. Most times there is a harsh edge to the sound or perhaps with some a rolled off high frequency and a bloatey bass. This harshness or colouration is a result of ampliifer distortion characteristic of the design of the ampliifer - which leads to listening fatigue (a common term in the audio industry used to describe becoming tired and disinterested when listening to amplified music.
Designing an amplifier without listening fatigue necessates a fundamentally different approach to design. All amplifiers create distortions which the brain must contend with by relying on memories of these instruments or events to make sense of them. The brain knows something is not right but tries really hard anyway to correct the perceived sound. Ultimately the brain tires of this profound exercise, looses interest and you then turn off the music.
With a Tenor amplifier, you experience only the music - unimpaired by any listening fatigue. The naturally low distortions of a Tenor amplifier are carefully mapped with a proprietary circuit (see HSI for further reading) that presents the harmonic structure that brain listens effortlessly. Your perception is zero distortion. This technology is the result of over 40+ man years of research and millions of dollars of investment. We think it was worth it and think you will too!
Build
Consumed with perfection, Tenor’s relentless pursuit makes the smallest of details a major importance...
Some examples of this pursuit:
A Washer:
A fanatical path filled with obsessive detail such as the washer used in the mounting techniques for the mosfets in the output modules.
Discussion: "When the device is tightened, we use a special tool and a custom cupped washer to precisely adjust the pressure against the heat sink. Everything is calibrated including the beveled washer. The screws are designed to work to specification and the beveled washer maintains a constant pressure on the transistor in contact with the heat sink. Specifically, the washers are calibrated so that when the cupping curvature is flattened, the washer itself will exert a known and fixed compression on the mosfet. For example, a fully compressed washer might exert a pressure of 5psi. In actual construction, the washers are never fully flattened but adjusted for a specific working tension. If you screw directly onto the aluminum, the MOSFETs and the heat sink could expand at different rates and cause stress over a period of time. With our washer, you will maintain constant pressure and contact - forever."
A Screw:
Simply a screw: "Even our screw costs three times the amount of the standard screw. The head is perfect, threads are finer quality, the finishing is better and we quality control every single one. A typical screw has a slight roundness to the head and is not perfectly flat, which in this case would cause imperfect contact. Our screws are perfectly flat. The screw was designed to mate perfectly with the beveled washer. We experimented with six different washer and screw shapes before deciding on the current ones. A fortune in time and labor..."
Compulsive behavior:
Being compulsive about a screw and a washer continues with all areas of a Tenor product. For example, the Line 1/Power 1 preamp uses the single most expensive volume control in the world The buffer stage (changes voltage to current for driving cables) is done without any distortion whatsoever using selecting transistors whose natural distortions are exactly the reciprocal value of each other transistor. The result - zero distortion!
The Line 1/ Power 1 took almost 5 years and $1.5 million dollars to develop. The result is breathtaking!
With Tenor there is never a thought of compromise.
Tube details:
At Tenor we go to extraordinary lengths. By designing a proprietary tube testing chamber to measure distortions of tubes we can match each tube perfectly to its intended circuit. Also, all tubes exhibit some level of microphony so Tenor has built a mini anechoic chamber with a wideband speaker to inject near field noise into the tubes. The internal vibrations amplified by the tube are analyzed with an oscilloscope, voltmeter and spectrum analyzer. Tubes exceeding a test threshold are rejected. Since microphonic can worsen over time, all tubes are tested only once they have been burned in for several hundred hours and tested for shock resistance, DC characteristics, gas transconductance and current. A 60% rejection rate on some tubes is possible but generally 7% - 15% is more the norm.
Vibrations/RF/Tolerances:
Tenor obsessively controls vibrations using multiple stages of decoupling via wood and rubber in the feet, internal board mountings, suspensions and dampening material on the interior surfaces. For example, the audio board suspension of each amplifier is designed for a resonant frequency of 20Hz to isolate floor borne bass vibrations and microphony effects.
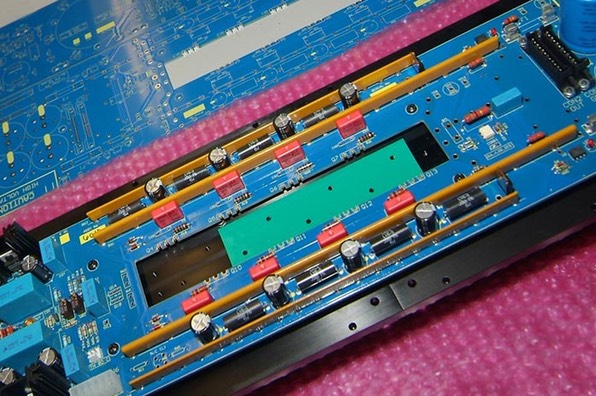
Circuit boards are shielded against airborne Radio Frequencies (RF):
The majority of internal wires are silver-plated copper with Teflon insulation for stability and superior insulating properties with a low dielectric constant. Special oil is used during the extruding process and the combination guarantees that this wire will not oxidize even after 20 years. Similar wire is used in critical aircraft circuits. With Michel’s background in military aviation, one see hints of this in the wires, shielding, bundling and other electrical components such as:
- Electrolytic capacitors are spec’d to 105°C (221°F) for long-term reliability.
- Film capacitors are selected and tested for distortion.
- Resistors are selected for a variety of parameters including temperature stability, voltage coefficient and the abilities to sustain transients without creating distortion or failure.
- The PC boards are 1/10th of an inch thick with 3 ounces of copper per square foot, which is very thick. This allows narrower trace widths to reduce capacitance effects.
- The cables are measured and selected to eliminate parasitic voltages from signal transmission or vibrations.
- The fuse contains a ceramic tube silver wire surrounded by sand to prevent the wire from dissipating heat. Therefore the fuse blows very quickly in reaction to an overload and is carefully placed in the circuit to eliminate distortion caused by the fuse itself.
- Cardas connectors are used throughout.
- Internally the unbalanced connections use a special cable and connector from the microwave industry made from copper and silver, with Teflon insulation and ultra-stable SMB connectors for reliability.